- February 9, 2017
- 2 Comments
Complete Guide to Butt Joints (Wood & Welding)
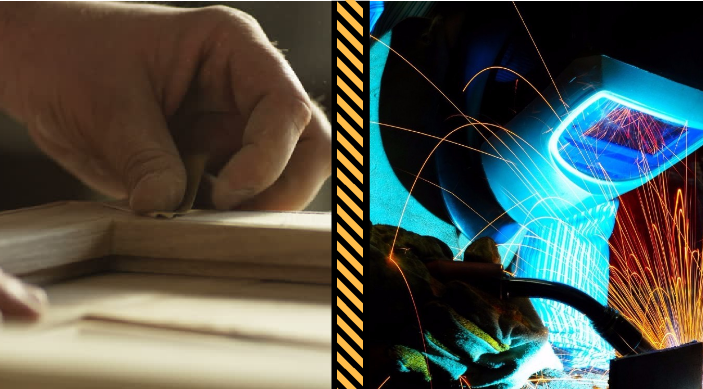
There’s nothing like that feeling when you fill the gap between a butt joint.
Whether you’re in Welding or Woodwork the butt joint is a simple, but necessary, addition to any craftsman’s arsenal of joints.
If you’re just starting out, a butt joint will probably be the first joint you’ll learn and is one of the best for practicing your crafting skills.
This article goes in deep and will cover all the different types of butt joints in both woodworking and welding.
Butt Joints in Woodwork
In woodwork, a butt joint is simply two pieces of timber that are butted together at each end.
A wood butt joint is weak and often hideous to look at. Most other joints, such as a corner or finger joint, are much more aesthetically appealing and physically stronger in frame.
Because of its weak nature, many craftsmen reinforce their butt joints in various ways. Some opt to nail their butt joints, others prefer screwing them and the really old school artisans like to stick dowels between their butt joints.
Nailed Butt Joints:
Reinforcing a butt joint through woodwork involves driving several nails through both pieces of wood, securing them in place. In the construction industry, nailed butt joints are regularly used in platform framing. At a smaller scale, nailed butt joints are also used in making cabinets and wooden toys.
In this process, nails can also be replaced with screws (called a screwed butt joint) and glue may also be used for added strength. In these methods, it’s important to sink the nails/screws into the wood to avoid them blocking any sections.
Dowel Butt Joints:

A dowel reinforced butt joint is one of the most widely used joints in furniture making (chairs, cabinets, tables) and is likely the first joint you’ll learn in any woodworking class.
This method of reinforcement is done by accurately drilling a series of holes in the surface of each member. Accuracy is the most important step of this process, if they are not aligned the joint will be uneven.
Once the holes are drilled, glue and dowels are inserted to the joint, then clamps are attached to hold the members together. Clamps are temporarily used while the glue is setting because this ensures that the joint is tight and secure, and so the glue sets properly.
Biscuit Butt Joints:
A recent innovation, Biscuit reinforced butt joints are similar to dowels in that they involve using an additional piece of wood and glue to join the members together.
As the name hints, the difference here is that dowels are instead replaced with biscuit shaped pieces. An advantage of this process is that once glue is applied and the piece is clamped together, the wooden biscuits absorb moisture in the glue and swell up creating a perfect fit.
These joints are generally used in furniture construction and are beneficial as they are a more convenient alternative to the dowel predecessor. Accuracy is not as important with biscuit joints, with the distance between each face being more critical.
Butt Joints in Welding

In welding, Butt welds are used to connect two parts that are parallel, without having them overlap.
This is normally done manually, using an arc or MIG welder, and works by slowly heating up each end of both plates. The plates are then joined together when a specific temperature is reached (depending on the metals used).
If an arc weld is used, waste material (slag) must be removed with a hammer forge. MIG welding on the other hand, uses a protective gas insert, protecting the purity of the weld and thus no slag appears.
If you’re new to welding, you can read more on Arc and MIG welding in our Basic Welding Guide.
This process can also be done in an automatic setting, using industrial strength clamps-then heating and bringing them together. In manufacturing, this method is faster and more efficient.
What’s more, butt joint welding is economical, reliable and comes in a few joint variations, depending on the metal thickness and shape. These being: square butt joint, and Single V and Double V butt joint.
Square Butt Joint
Generally used for metals 3/16 inches or less in thickness, a square butt joint requires minimal preparation as it simply requires matching the flat edges of the plates together before welding.
Squared butt joints are a strong weld, although user guides don’t recommend this method for metals subject to fatigue or impact. This is where V butt joints are utilised.
Single V and Double V Butt Joints
Used for metals 1/4 to 3/4 inch in thickness, a Single V joint involves bevelling the one edge of the pieces to allow room for filler material (an electrode)- this gives the joint the strength required for any loading or impact.
These grooves are made with special bevelling machines or a cutting torch and is a stronger joint than the squared butt weld.
A Double V butt joint works under the same concept, although both edges are bevelled and is ideal for metals thicker than 3/4 inch.
Achieving a good quality V joint involves taking the time to properly inspect the material thickness, type and design.
—
In the market for welding supplies?
For everything from Helmets to Purge Monitors visit here.