- October 26, 2022
- No Comment
How Many New Mines are Needed to Resource the Future of Renewable Energy?
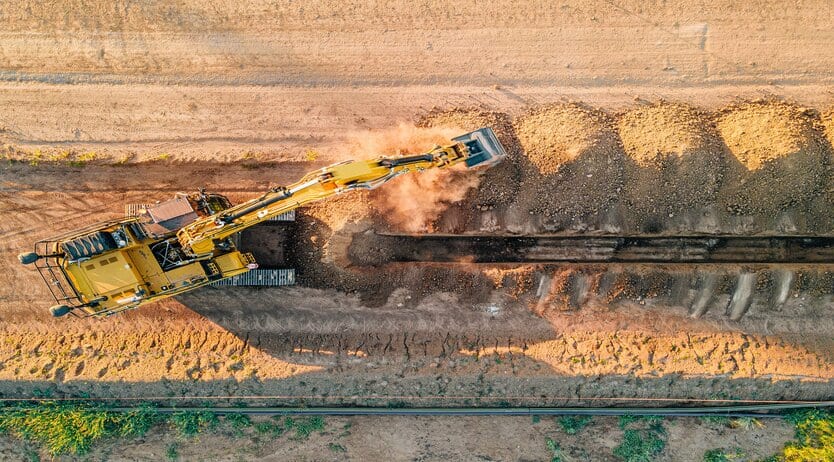
Presented by Pickles
Some experts suggest over 300 new mines need to be developed in the next decade to facilitate the switch to electric vehicles and renewable energy.
The electric vehicle (EV) and renewable energy booms are both exciting movements in the direction of realising ‘net zero’ plans. But is this sustainable transition realistic in the timeframe that many experts are forecasting? Judging by data in fig. 1, probably not. However, the growth of innovative solutions in the mining industry may be able to aid the transition while still assisting operations. This creates a new challenge for the mining industry. Exploring for and extracting resources fast enough, and in quantities great enough, that meet the ever-increasing demand of raw materials for providers in the EV and renewable energy sectors.
Broad Demand Outlook
With the race to ‘net zero’ becoming a universal focus by countries and conglomerates alike, supply chain considerations are now at the forefront of manufacturers’ minds. A report released by the International Energy Agency (IEA) suggests that the supply of battery and mineral supplies will need to increase tenfold by 2030 if we are to meet government EV goals alone – see figure 1.
Figure 1: Number of mines to produce required levels of metals asset. Source: https://iea.blob.core.windows.net/assets/4eb8c252-76b1-4710-8f5e-867e751c8dda/GlobalSupplyChainsofEVBatteries.pdf
A tenfold increase in mineral supplies is no easy feat. Benchmark, a mineral intelligence agency, has researched the number of mines that will be required for each resource to meet these demands – see figure 2.
Graphite
Graphite is going to be the most sought after resource with the largest number of new mines and plants needed to feed demand for anode materials. There are two types of graphite that will be required – natural and synthetic.
It’s estimated that 97 natural flake mines will need to be built and in operation by 2035, assuming an average mine/plant size of 57,000 tonnes. That means that by 2035, 7.2 million tonnes will need to be available for the battery market, up from 2.1 million tonnes in 2022.
From a synthetic graphite standpoint, which is produced using pet needle coke or coal tar pitch, 54 plants with an average production size of 57,000 tonnes must be available by 2035.
Lithium
Lithium, the favourite of the EV industry and often regarded as the 21st Centuries ‘Gold Rush’ item, will be a dominant factor in meeting the demands of battery and EV manufacturing. In 2022, lithium supply reached 678,000 tonnes, a record for extraction in a year. However, this quantity seems insignificant compared to what demand will reach in 2035 with 4 million tonnes of the resource projected to be required, equating to around 74 new lithium mines with an average size of 45,000 tonnes by 2035.
To achieve this monstrous goal, its estimated $7 billion will need to be invested each year until 2028 to meet demand. Should this level of investment fail to be achieved, recycled lithium is set to make up the shortfall. Thanks to a new promising recycling method where the refurbishment of a cathode takes place, batteries can perform on par with, and in some cases better than, new batteries.
Nickel and Cobalt Nickel and Cobalt are set to double and triple in demand respectively. For nickel, 72 new mines with an average size of 42,000 tonnes will be necessary. Cobalt on the other hand will need 62 new mines with each producing 5,000 tonnes of the mineral each year. Recycling initiatives however are set to bring the need of Cobalt mine numbers down by almost half to 38 new mines.
Figure 2: How many mines do we need – graphic. Source: Supplied.
Copper
Copper is another crucial resource for supporting the growth of the EV and renewable energy market but also maintaining demand for traditional uses like construction, transportation and telecommunications. From a demand perspective, a rather scary forecast has been formulated which predicts around 700 million tonnes will be required in the next 22 years alone, the same amount that humanity has consumed since 4000BC – see figure 3.
To meet this colossal figure, it’s estimated around $100 billion will need to be invested by 2030. To put that into perspective, the largest copper mine in the world – Chile’s Escondida – produces 1.4 million tonnes annually, more than the world’s second and third largest copper mines combined. Meeting this demand means building just under two Escondida mines every month over the next 22 years.
Figure 3: World consumption of refined copper. Source: United States Geological Survey, BMO Captial Markets
Lead times to hamper growth
Identifying the need for more minerals is only the first step, getting these mines up and running is a whole new challenge in itself. Lead times will be the biggest hurdle the industry will face. Once the exploration phase has been completed with regions identified as being extractable, the huge task of setting up a mine for production begins. On average, it can take anywhere from 4 to 20 years – see figure 4 – for a mine to commence extraction with the majority of this time dedicated to feasibility studies, engineering and building of mining infrastructure.
Figure 4: Ranging of typical lead times for initial production for selected steps in EV battery supply chain. Source: IEA analysis.
Innovative Solutions for extraction capacity and lead times
Building new mines is a longterm solution for the establishment of a secure supply of important EV and renewable energy resources. With the need for these minerals reaching urgent levels with future shortfalls predicted, alternative solutions will need to come about to assist with propping up supply.
One solution for the novel extraction and processing of lithium is Direct Lithium Extraction (DLE). DLE can increase production from existing mines by bypassing time-intensive evaporation and chemical removal of impurities. DLE technology removes lithium and associated anions from a brine solution and shifts it into a different medium, such as water, for further processing to final products. Not only is this a cost-effective approach with lead time benefits thanks to a widening pool of extractable lithium that offers sustainability advantages too.
Nickel can also be produced quicker and at quality grades thanks to High Pressure Acid Leaching (HPAL). HPAL uses acid separation under high pressure and temperature to effectively yield Class 1 grade nickel that is suitable for battery application of laterite resources. However, HPAL comes with issues ranging from capital costs, which can be double that of conventional smelters, to environmental concerns where up to three times more greenhouse gas emissions can occur due to the heat that is required.
Mixed Hydroxide Precipitate (MHP) is another solution which is an intermediate product produced from laterite, an iron and aluminium rich mineral, that can be refined into nickel (typically 34-55%) and cobalt (1-4.5%). The intermediate is primarily produced at operations that utilise HPAL to extract nickel and cobalt from low-grade laterite ores.
With the recent rally in copper pricing, miners of the resource are evaluating the economic feasibility of extraction from tailing dumps. It’s estimated there could be as much as 43 million tonnes of copper sitting in waste dumps at mines across the globe – equivalent to a decade’s worth of mine supply. A Canadian start-up, Jetti, has developed a catalyst that can release copper from low-grade chalcopyrite ores by disrupting the sulphur metal bond of the mineral.
The EV and renewable energy sectors are becoming hungry, mineral consuming giants that current mining practices are struggling to keep up with. To suggest that miners need to build some 300 mines in the next decade to keep up with demand is an impossible task. Not only because the money, resources and manpower required would be monumental but also because lead times for the set up of these mines could take up to a decade to build and become fully operational. Time which EV makers and the renewable energy sector don’t have. Innovative solutions therefore, in conjunction with new mines, will play a huge role in helping unlock additional supply which hopefully will fulfill worldwide demand for years and decades to come.