- June 16, 2017
- No Comment
Welding Automation: Amazing to Watch but Worth the Investment?
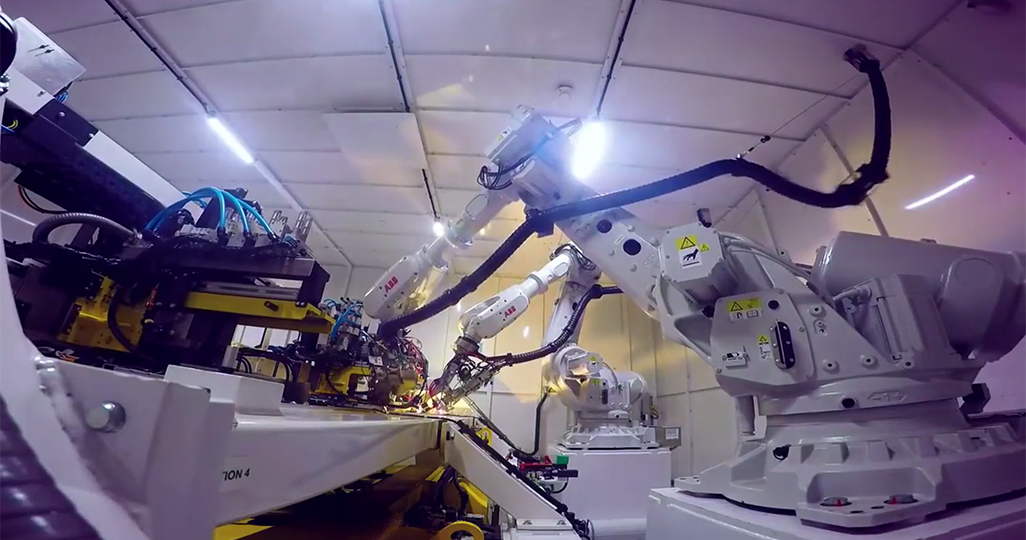
Apart from being a mesmerising process to watch, robotic welding offers a range of benefits for those with the resources to make the investment. However, skilled humans are still a vital part of the welding world (and will remain so for the foreseeable future).
While many businesses would see a massive benefit from switching to a fully automated system, others would be more suited to the semiautomatic options available and still others are better of sticking with the flexibility of a human operator.
Fully automated welding
Fully automatic welding involves any configuration from a single custom unit to a series of machines (as you can see in the video above) flowing through the work in a perfectly choreographed robotic ballet. The machines take care of everything:
- loading the work piece;
- indexing the torch (or part) into position;
- completing the weld;
- quality assurance of joints;
- unloading the final product.
While the machine is responsible for the whole process, some setups do require a human operator for certain aspects of the work.
Products best suited to fully automated welding systems:
Anything precise, repeatable and high volume, such as:
- pipe fittings;
- valve elements;
- batteries;
- solenoids;
- light bulb elements;
- transducers;
- transformer cores;
- fuel filters;
- metal bellows.
Semiautomatic welding
Here, humans and machines work together but their participation levels in the work are far more equal than the human-machine relationships of the past. Rather than being a mere tool, the semiautomatic welding system is more of a robot coworker. Its human counterpart loads the parts and programs parameters but the machine takes care of:
- the welding process;
- torch motion;
- maintaining the position of the part.
The human then steps back in, removing the completed component before loading up the next project for the machine.
Best candidates for semiautomatic welding systems:
While accurate, repeatable and high volume designs are still an important consideration for semiautomatic welding systems, there is a bit of leeway for products with more complexity or variety as the machine can be used to take care of the simple repeatable aspects and the human can take care of the less straight forward work. While the machine has to stick to its highly specific presets, its human coworker can shift between part types and equipment in a flash (terrible welding pun intended), thus maximising resources.
The semi-automatic welding system is also better suited for manufacturers with smaller product runs which would benefit from automation but not enough to justify the expense of a fully automated system.
Benefits of Automated Welding
Both the fully and semiautomatic welding systems have a host of benefits to offer in exchange for the cost of installation. Predominantly, you’ll be looking at an increase in weld quality and output and a decrease in scrap and labour costs.
Weld quality and automation
With their electronic weld process controllers, the parameters for each programmed job are precisely maintained by the automated welding machines, giving you a consistently higher quality weld than can ever be attained manually. On top of this natural quality control, the machines can be programed to enact further quality checks and are incapable of even being aware of the infinite distractions humans are at risk of falling prey to.
Even if a defect does occur, because the automated systems do their work in a uniform manner, any discrepancy is immediately evident. The robot will never attempt to smooth over or hide its faulty work.
Taking the ‘man’ out of manufacturing
With set parameters, higher weld speeds and no need to rest, take breaks or check its phone, an automated welding system will have no issues out competing even the most skilled human welder. As a human becomes tired, the likelihood of error rises. Not so with a mechanised welding rig. The machine will only commence the weld when all parameters have been perfectly aligned. This means a reduction in scrap and avoidance of the possibility of shipping a defective part to a client.
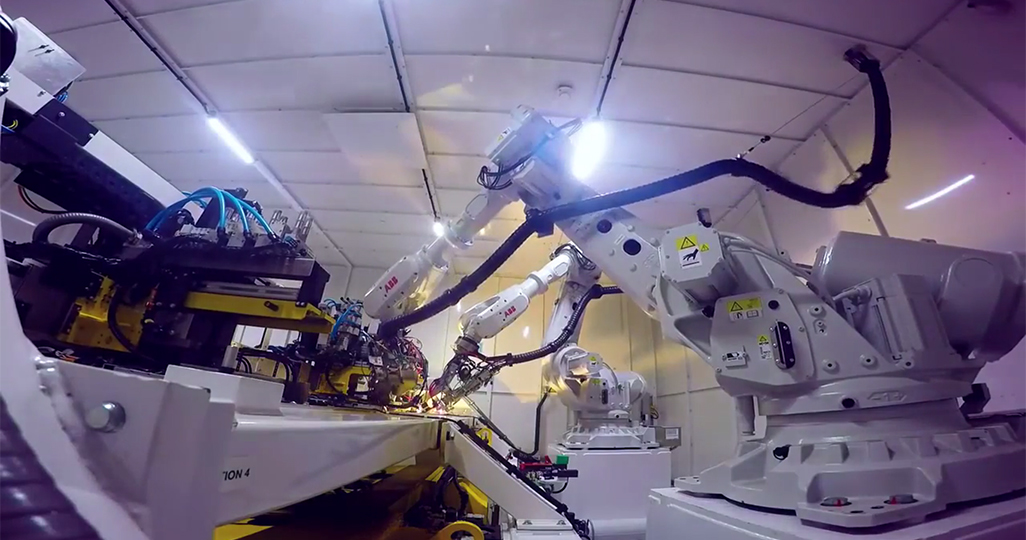
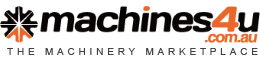