- January 6, 2023
- No Comment
5 Things To Consider When Setting Up Your Timber Joinery Factory’s Compressed Air
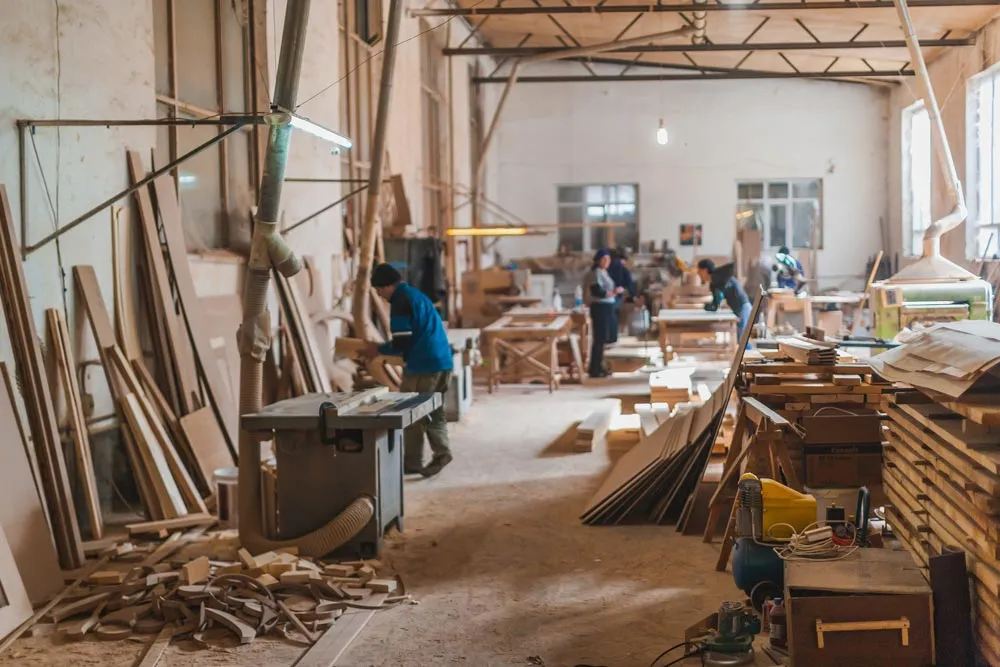
Presented by Focus Industrial
When setting up a timber joinery factory, there are several important factors to consider in regards to compressed air. These include the size and type of compressor, piping size and material, system layout, filtration and regulation equipment, and ongoing maintenance. Proper planning and installation are crucial for a reliable and efficient compressed air system.
1. Size of the Compressor
This is the most common question when setting up joinery factories because of the variation of the compressed air consumptions with different brands of wood working and timber processing equipment. This is very important to get correct as the equipment and machinery that uses the compressed air are very sensitive to correct air pressure and flow. If the compressor is undersized, it will cause the machinery to cut out causing significant disruptions to the operation and the compressor will overwork if it is a piston compressor causing premature wear and failure. If the compressor is oversized too much it will underwork and cause the same issue of premature wear and increase power consumption.
A critical factor to consider when sizing your compressor is the expected growth. This can be hard to get accurate however if you have plans of adding more CNC machines, Edge banders or other equipment it is important to factor these additional machines into the air demand. Click here to access a guide for air consumption for timber joinery factories where you can put in the equipment you have. This will give you a guide for what size compressor you would need. Remember the guide measures average consumptions taken from a variety of brands of timber equipment so it is important to get clarification of your result.
2. Piping Size and Material
Choosing the sizing the correct compressed air piping size is as important as the compressor itself. You can have the correct sized compressor you have invested significant money into, and it can be a total waste with an incorrect sized compressed air piping system. While every workshop is different in layout and design, we recommend for any joinery shop running a CNC, Edge bander and a few hand tools for up to 50m of piping to install a minimum diameter piping of 25mm.
Once additional machinery is added larger diameter piping should be installed to ensure as minimal as possible pressure drop as possible between the compressor location and the point of use at the CNCs. There are various common diameters of compressed air piping available which include:
- 20mm Compressed air piping
- 25mm Compressed air piping
- 32mm Compressed air piping
- 40mm Compressed air piping
- 50mm compressed air piping
- 63mm Compressed air piping
- 76mm compressed air piping
- 90mm compressed air piping
- 110mm compressed air piping.
It is important to speak and consult with an expert on what size piping you would require in your factory setup to ensure a reliable and effective compressed air system.
There are also several options with the piping material such as Poly piping, Aluminum piping, Stainless Steel piping and Copper piping. Each of these different materials have their advantages and disadvantages. Commonly poly piping is used in small to medium compressed air systems because of the cost benefit and simplicity of installation. Aluminum is also reasonably easy to install with the Uni pipe compression fitting system however costs a reasonable amount more than a poly system. You will however get an easy adaptable pipe system with a neat and clean finish with all piping sitting straight. The stainless steel and copper systems are commonly used with medium and large setups. With the Sure press stainless steel piping system coming with a 25 year no leak guarantee this is a very solid investment.
A lot of larger companies are now using this as the savings in power costs against air leaks give a good ROI and give guaranteed reliability. These systems do require a specialist pipe crimping tool however which puts it often out of the DIY range of compressed air piping.
3. The Compressed Air Layout
The layout of the compressed air system is a vital part of ensuring your compressed air system works. What is often overlooked like the piping size and material. The most Important thing with choosing your route for your compressed air system is to find the most direct path to the equipment. This reduces the flow time from the compressor location to the machinery requiring the compressed air and guarantees a better and equalized pressure throughout the system.
The second most important tip is in the location of the compressor in conjunction with the machinery. While there are many other factors involved in the correct location of the compressor it is important to locate the compressor closest to the machinery that consumes the most amount of compressed air. Thirdly the importance of a ring main in your compressed air system is often underrated especially for medium to large systems. This value of a ring main is it gives much better pressure and flow equalization meaning every area of your factory has consistent air pressure.
4. Compressor Location
The compressor location is very important for both the lifespan and reliability of the compressor and the guarantee of a well-functioning and efficiency compressed air system. Often a compressor is tucked away in the back corner of the factory or put outside in a lean to with extreme conditions impacting the longevity. With every factory setup different, there is no correct one answer fits all. In saying that, below is a list of key points to take into consideration when deciding the correct location for your compressor.
- Where the location of the highest compressed air demanding machinery and equipment is in the factory,
- The ventilation, has the compressor got sufficient ventilation
- Environment, is the environment clean and dust free
- Power supply, is there sufficient power supply nearby where the compressor is going to be located?
- Weather. Is the compressor in an out of weather area that is protected extremes such as rain and sun. It is important especially in Australia to ensure the compressor is not in the afternoon summer sun as this will cause the compressor to overheat.
5. Future Proofing
Future proofing your compressed air capacity is important to ensure you don’t have to reinvest prematurely. While visions and forecasts are always important to assist in the correct sizing of the compressor, its not easy and no one has perfect vision of the future as everyone found out when Covid19 came upon the world. When we assist customers with their compressor system, we usually try to get an accurate indication of what their expected growth and changes are going to be in the next 5 years. This usually gives enough of a timeline for what the customers are going to do and we can accurately size the compressor without oversizing. While making the investment its important if you have rapid growth plans to discuss it with us so we can set up a plan to help you set up your compressed air system as efficiently, effective, and economical as possible for not just now but into the future also.
In conclusion, setting up a timber joinery factory compressed air system requires careful consideration of several factors, including the size and type of compressor, piping size and material, system layout, filtration and regulation equipment, and ongoing maintenance. Proper planning and installation can ensure a reliable and efficient compressed air system that supports the smooth operation of the factory.
For more information about compressed air systems in general, or to ask about a specific product that we provide contact us via our showroom.