- June 26, 2017
- No Comment
Take Your Woodworking to the Next Level With These 5 Expert Tips
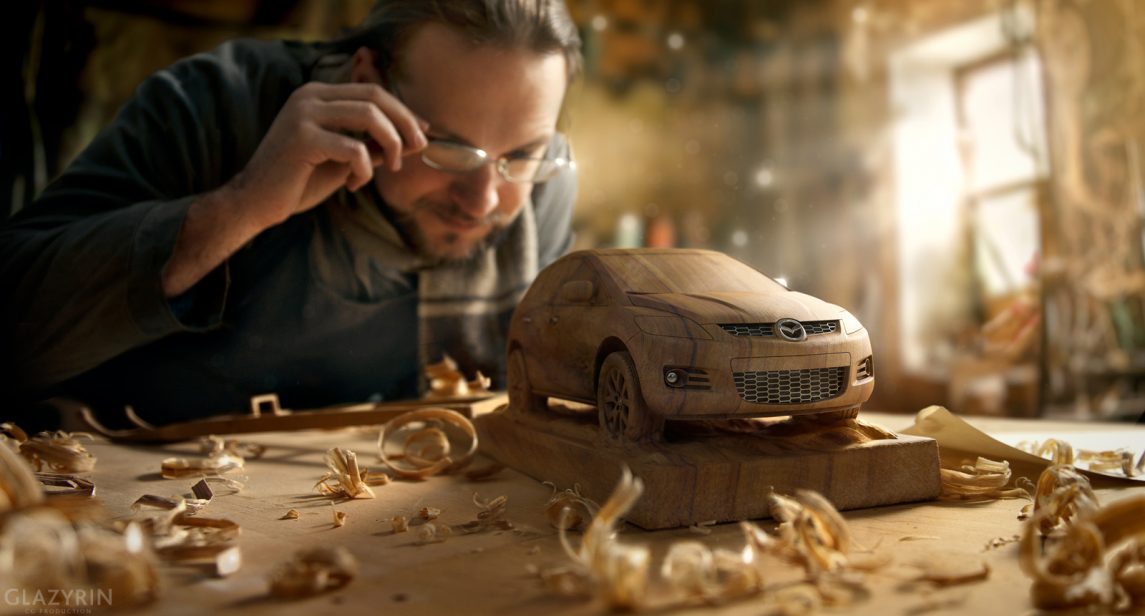
The Machines4U team recently got to spend some time with master woodworker, Steve Hay. Rather than going for the quick and easy ‘tips and tricks’, we delved deep to bring you some golden pieces of advice that mark the difference between an amateur and a master woodworker.
#1: Add some zen to the art of woodworking
As a society, we are phenomenally obsessed with speed. Every second saved is an achievement and time is becoming a commodity almost more valuable than money. Yet, for all our fast cars, fast food and fast internet, we are also responsible for the invention of the word ‘time-poor’.
With a multitude of things we want to achieve, many of us feel strapped for time. And, even on weekends, it’s tempting to boot up another coffee and get cracking on as many projects as you can manage. According to Steve, this caffeinated approach to life has no place in a woodworker’s studio.
“I think people, they’re in a rush nowadays, they want to start a project, and they wanna finish it in the same day. And I can relate to that. I’d love to do that. But unfortunately, you can’t. You’ve got to take time.”
And this shouldn’t be seen as a drag. Quite the contrary. A woodworking project is your opportunity to inject a little zen into your life. While working, you get to ignore distractions and focus on the slow development of your creation. Think of it as a moving meditation that doesn’t involve hippies and chakras but is just as regenerative for the overworked modern mind.
#2: Learn to use hand tools
Woodworking machinery is fantastically useful for speeding up the non-creative aspects of woodworking. However, Steve warns about relying on machines for every aspect of your work.
“The finesse is in the hand tools. I’ve got all the machines, but my way of thinking is, machinery is to remove waste so I can get to the workbench quicker and use hand-tools.”
Steve isn’t speaking from a preconceived bias here. He’s gone to the trouble of conducting comparative experiments, creating the same project twice; once with hand tools and once with machines. He’s done this with a number of projects and, for joinery and finer work, always comes back to the hand tools.
“I have far more control over them. I can think, I don’t have to worry about losing my fingers! And if I make a mistake I can stop it very quickly. Whereas, if you make a mistake with a tool bit traveling at 22,000 RPMs, it’s generally a bigger mistake than traveling a foot a second with a molding plane.”
#3: Invest in quality tools and machines
There’s a time and place for bargain-bin purchases and woodworking is never anywhere near it. Unless you’re one of those masochistic types who enjoys being frustrated. According to Steve, many people lose confidence in their woodworking skills, thinking they’re ‘just not getting it’, when in reality, it’s cheap tools and machinery they’re using that’s holding them back.
“And there is a glut on the market. Machines that are built to a cost, to a price, and not a quality level. It’s the same with hand tools. A lot of my hand planes are worth upwards of I don’t know, $500? $1000? And people go ‘oh, no I can buy one from the supermarket for $14.99.’ Well, yeah, you can. But it’s not gonna work the same.”
If budget is an important consideration, Steve suggests, you’re far better off looking for good quality woodworking tools and machines second hand. This way you can save yourself some cash without sacrificing in quality.
#4: Learn proper joinery
With the range of glues available nowadays, it can be tempting to just believe the grandiose claims on the packaging, glue up your joins and think that’ll be that.
“It just distresses me. When I see people making stuff, and they put so much effort into it but they’re doing it wrong. If you don’t allow for the expansion and contraction of the wood in your design, then the glue joint is gonna fall, pop out, or split the timber.”
Wood is a living thing and, even after the tree has been turned into timber and crafted into furniture, in its own way, it continues to breathe. Steve explains:
“Stuff they’re pulling out of the pyramids will still expand and contract. Even though the tree’s been cut down, it’s still basically a living organism.”
On the microscopic level, wood is made up of strands and strands and strands of tiny tubes. When humidity drops and the ambient temperature rises, moisture leaks out of the tubes and they collapse and shrink, like squeezed up drinking straws. Then, with humidity or rain, wood’s hygroscopic nature means it will absorb the water in the atmosphere and bulk out its straws.
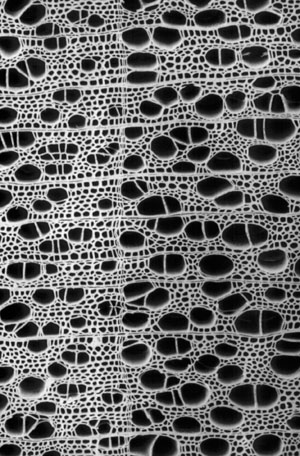
All the master woodworkers understand this and work the expansion and contraction of the wood into their design and craftsmanship. In no place is this more important than joinery.
“The art of furniture making involves making joints that fit together so nicely, that really, you don’t need glue.”
#5: Know your wood
The more you understand about the wood you’re working with, the better your creations will be. There are so many elements that influence what a piece of timber is best suited to be made into. It’s density, grain, colour, even its smell. Some of Steve’s favourite smelling timber types are New Guinea and Australian rosewoods, scented gum and coachwood which he describes as:
“just like hot caramel sauce.”
While your knowledge will be built empirically through research and experience, all the master woodworkers seem to develop a more subtle, intuitive connection to timber as well. Almost like a whole new sense.
In his exceptional woodworking manual, A Cabinet Maker’s Notebook, master woodworker, James Krenov, remarks on the ‘relationship’ you build with the timber that sits in your workshop. It may sit there for years, in quiet contemplation, before it finally ‘tells him’ what it wants to be made into. Steve reports this same sort of connection to the materials he works with.
“That’s something you can’t teach either. You just gotta be sympathetic to the environment you’re working in.”
If you’re using Steve’s number one tip and developing a sense of zen with your woodworking, this connection with the wood will follow. And, if the timber is talking to you, there’s no need to worry about your sanity.
“If it makes me crazy, well, it’s my type of crazy, you know? I’m happy with it.”
—
More articles featuring Steve Hay’s tips…
- The Complete Guide to the Humble Hand Plane
- Expert Advice on Getting Wood in the Wild
- How to Use a Sharpening Stone: A Lesson From the Masters
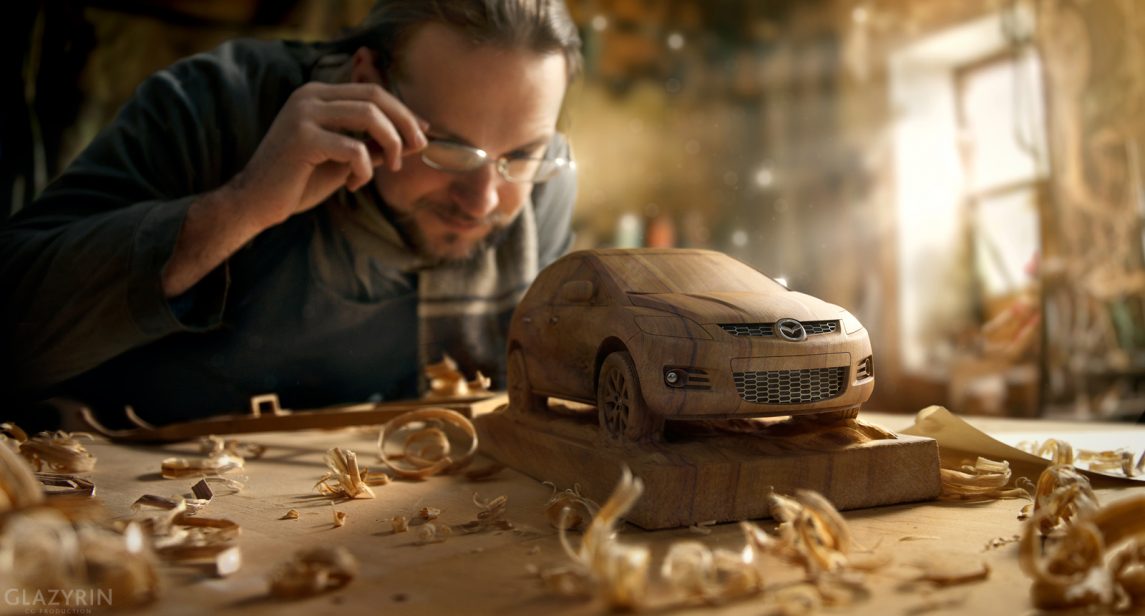
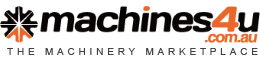