- February 11, 2017
- No Comment
Welding Cast Iron: The How-To Guide
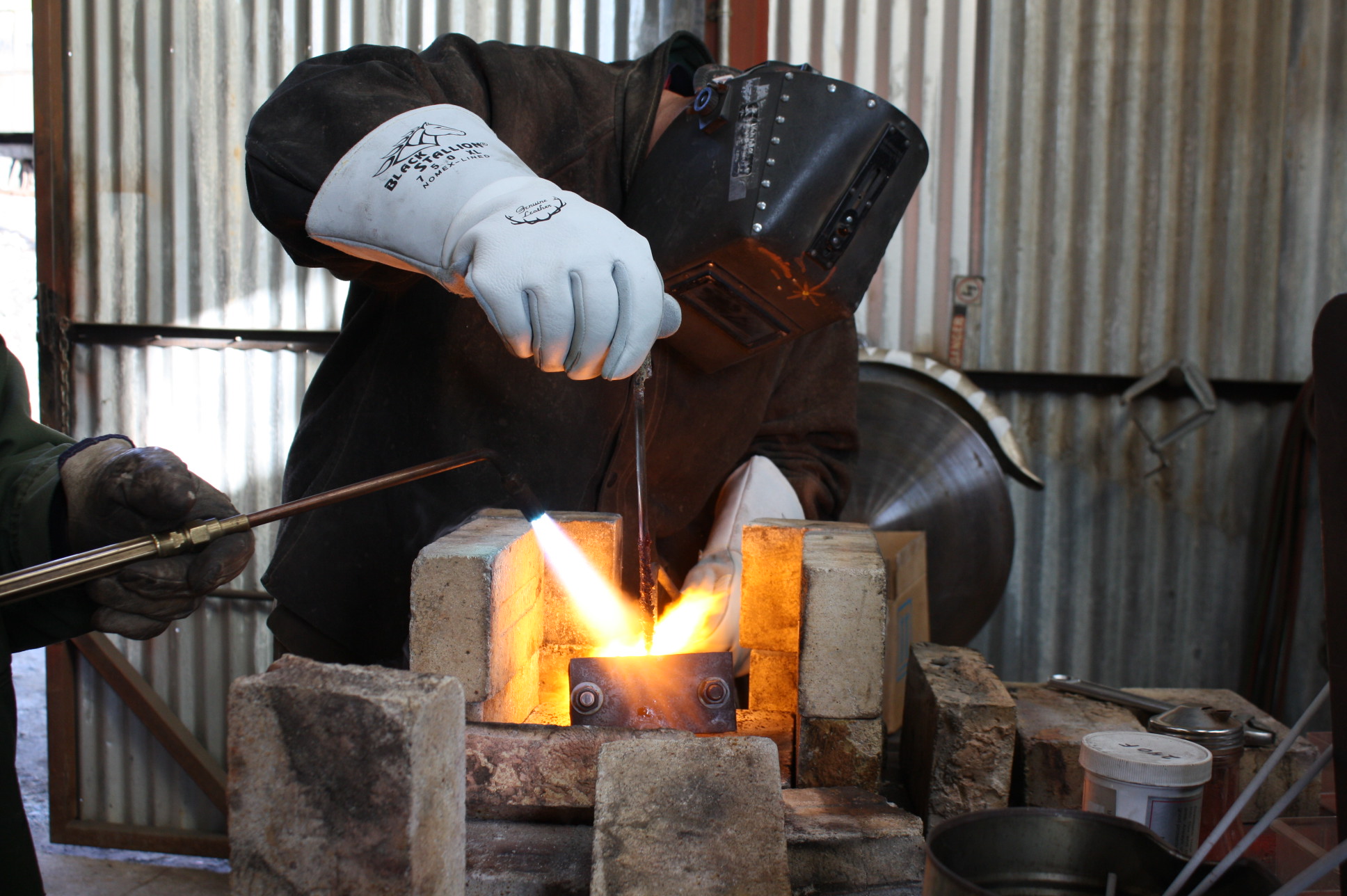
Cast Iron. It’s brittle, cheap and a pain in the ass to fix… but we use it everywhere from the workshop to the kitchen.
If you’ve found a crack, cut or crevice in a cast iron piece and you’re handy with a welder, there’s a good chance you can repair it. You’ll just need patience and a bit of know-how, this article will give just that, outlining all the information you’ll need when repairing that cast iron piece.
Can You Weld Cast Iron?
When it comes to welding cast iron it’s important to understand the difficulty of the job. It’s more than likely you’ll end with up with more cracks in the piece than you started with and the job generally has about a 50% chance of success.
Why?
Cast iron is made up of a number of different materials (normally iron, carbon and steel) at different proportions, this makes it’s hard to gauge just how strong the metal you’re working with is and how much heat it can withstand before cracking.
How To Weld Cast Iron:
Being brittle by nature, carbon contained in the mixture causes the metal to shrink and crack when heated past a certain temperature. Because of this, among other reasons, much care and attention is required before welding cast iron pieces. When welding cast iron, it’s important to account for:
- Pre- & post-heating preparation
- Heat management while welding
- Rod selection
To start, the process of welding cast iron requires 1. Beveling the fracture and 2. heating up the material. Explained in our Complete Guide to Butt Joints article, grooves, bevels or “V’s” are created on the piece with a special beveling machine or a cutting torch. This is done to ensure a stronger weld.
Pre- & Post-Heating Cast Iron Before Welding
Cast iron is very temperamental, pre- and post-heating is a must when working with cast iron. If the metal shifts from room temperature to welding temperatures too fast, the piece will experience too much stress and crack. The same goes for after the weld is complete, if allowed to cool down too fast the weld will also undergo stress and can fracture.
Pre-heating can be done simply by using your blowtorch to heat the material, some DIY welders even use a car engine to do the job. An ideal pre-heat temperature for most cast iron pieces would be between 260 – 650 degrees Celsius, anything over 780 degrees will overheat the material.
When post-heating the material, wrapping the object in an insulated wrapping blanked is ideal; though, a DIY welder could also use a Charcoal BBQ and sit the piece in a bucket of sand, or place the piece atop of a wood fire oven, allowing to cool down as the fire dies.
Welding To Repair Cast Iron
When welding cast iron, Low and Slow is a rule of thumb many welders abide by.
By this, operators should apply a low current and a slow movement (in a stitching like manner) when working with cast iron. Work at about an inch at a time, welding in different spots, and try to allow 45-seconds between segments to avoid both over heating and the buildup of residual stresses. Managing heat is the most important part of this process, it’s also beneficial to tack your welds prior to beginning.
Once a satisfactory weld is achieved, inspect for any cracks or slag holes. If there are small cracks next to the weld, leaking can be removed with a sealing compound or can even rust shut after continuous use.
If you’re in the clear, hit that bad boy with a slag brush and grind down any excess slag until smooth.
Now the your method of post-heating should be applied, allowing for a gradual cooldown of the piece.
Whats Better For Welding Cast Iron: MIG, TIG or Arc?
There is an endless list of ways you can weld cast iron, for the sake of this article, we’ll stick to the basics; MIG, TIG and Arc. In any of these methods, it’s important to remember the heat management and welding technique outlined earlier to achieve a good weld.
MIG Welding Cast Iron
While any professional wouldn’t recommend MIG over other forms, welding cast iron is very much possible with a MIG welder. Here are some tips we’ve found for MIG welding cast iron:
- The best choice in MIG wire would be specialty nickel wire, but this is the most expensive option, stainless steel MIG wire can also be used.
- An 80/20 (80% Argon, 20% Carbon Dioxide) gas works great in most situations, the only downside of this option though is the weld will rust eventually. Although, being cast iron the material is naturally prone to rusting.
- Using a brazing wire is possible of bond the cast, but is a weak weld and not suggested for metals that will experience impact or loading.
- Studding can be utilised to give mechanical strength to the weld, but this depends on the job.
TIG Welding Cast Iron
When TIG welding with cast iron, a nickel wire is the only real option available for this job. It can be expensive, but the TIG process can provide a strong and clean weld on most cast iron jobs.
It’s also possible to cold-weld (skip pre- and post-heating stage) cast iron with TIG, if you are using the correct gas, wire and settings. This process deserves an article in itself but here’s a short video outlining the process.
Arc Welding Cast Iron
Arc or stick welding is often the preferred method for many DIY welders. It’s simple and there is a wide range of electrodes available to suit different jobs, with many arc welders available for both commercial and domestic purposes at reasonable prices.
Generally, most structural repairs can be repaired successfully through brazing with a bare bronze rod, acetylene torch, and flux. Although in any welding situation, choosing the correct electrode often comes down to: cost, machine-ability, and whether the weld is a single or multiple pass.
What’s The Best Rod When Welding Cast Iron?
99% NICKEL RODS
Nickel based electrodes are often expensive and is considered the premium. 99% Nickel rods will produce welds that are machineable and works best on casting with low or medium phosphorous contents.
55% NICKEL RODS
A cheaper option, 55% nickel rods are economical. They too are machineable and is often used in repairing thick sections. It also has a lower co-efficient expansion than the 99% rod, meaning fewer fusion line cracks.
STEEL RODS
The cheapest option, steel electrodes, are best used for simple repairs and fillers. They are not machineable and produce hard welds, requiring some extra grinding to finish. A benefit though, is this rod is much more user-friendly when arc welding and can tolerate castings that are not entirely clean before welding.
Tips For Welding Cast Iron To Mild Steel
If a job requires cast iron to be welded to mild steel, stick welding is a great method to do so. A few tacks and some hammering with a slag brush makes this an easy job. Working at 95 Amps on DCEP (Direct Current Electrode Positive) will give great results.
How NOT To Weld Cast Iron
Finally, They say learning is best done after a mistake is made. One of the most popular welders in the world Youtuber, ChuckE2009, helps skip this step and shows why not all types of welding are meant for cast iron.